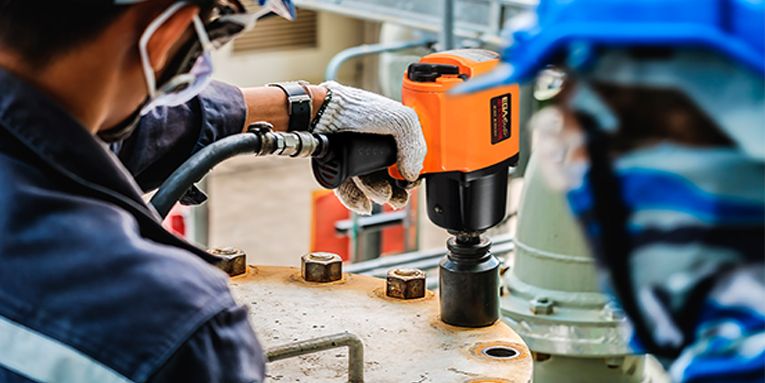
TIGHTENING PHYSICS
In threaded joint assembly regardless of method used, the purpose is used to obtain a clamping force that keeps the components assembled. The screw acts as a spring to the tension that generates such force and that is in balance with the parts it assembles, compressing them.
The rigidity of the screwed joint is determined by the force that the screws exert in the axial direction on the parts it joins. This force is characterized by the tension that is generated on the threaded shaft (bolt, screw) when tightened.
The optimum strength for each joint is determined by the function that it must perform, so the sizing, hardness and strength of the screws will depend on it.
Although the magnitude to be controlled is the axial stress of the screw, it is difficult and very expensive to measure. Therefore, there are several methods of controlled tightening, depending on the criticality of the measurement, the investment capacity, and the time available for the operation.
Do you want to know what these methods are? Read on!
CONTROLLED TIGHTENING METHODS
TORQUE CONTROL
This is the most used method, which is controlled by the applied torque.
ADVANTAGES
- It is a method easy to apply, fast and cost-effective.
- Due to the length of the screw does not affect the torque, the standardization is simple.
DISADVANTAGES
- The dispersion of the applied axial stress is large, and the optimum efficiency of the screw is not achieved.
ANGLE OF ROTATION
In this method the torque is controlled through the angle. The bolt is tightened to a specific angle from an initial reference torque.
ADVANTAGES
- The plastic deformation point of the bolt is reached, so the stress spread is small and the tightening efficiency is good.
DISADVANTAGES
- Because the elastic limit is exceeded, there are limitations to apply additional loads or perform re-tightening.
- It is difficult to calculate the required angle.
TORQUE GRADIENT
Here the property is used that, when the yield strength is exceeded, the deformation grows rapidly. Torque and tightening angles are detected with electrical sensors, the elastic limit is calculated by computer, and tightening is performed in the vicinity of this.
ADVANTAGES
- Reduced axial stress dispersion
- High tightening efficiency
DISADVANTAGES
- Equipment is very expensive.
- Not feasible in field work
ELONGATION MEASUREMENT
The elongation of the bolt generated by tightening is measured. This method can be carried out by micrometer or by ultrasound.
ADVANTAGES
- Dispersion is very low, so tightening accuracy at the elastic limit is possible.
- The tightening efficiency is high
- Additional loads or re-tightening can be performed.
DISADVANTAGES
- Equipment and time costs are high.
- Not very feasible in high tightening operations.
BY LOAD
Consists of stretching the bolt to the defined tension. In this method, it is the applied load that controls the tightening.
ADVANTAGES
- Axial tension is directly controlled
- No torsional stress is generated in the bolt.
DISADVANTAGES
- Both the loading equipment and the bolts are special.
- High cost of both the screws and the equipment.
BY HEATING
In this method the bolt is heated to elongate it. Tightening is controlled by temperature.
ADVANTAGES
- No space or force is required for tightening.
- No relationship between temperature and axial tension.
DISADVANTAGES
- Difficult to control temperature setting
- Requires preventive measures for handling hot parts.