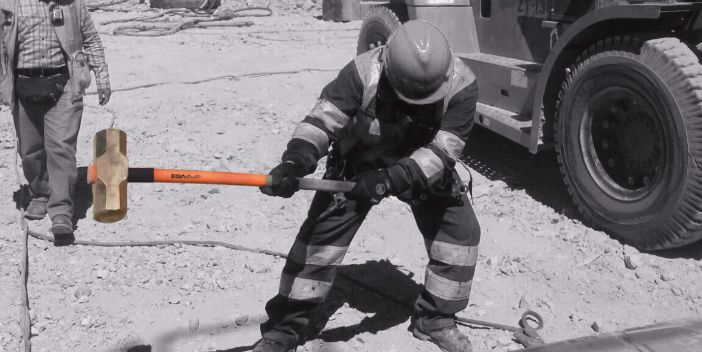
Safety in mining environments is of vital importance, and one of the key tools to prevent serious accidents is the explosion-proof mallet. These tools are essential to reduce the risk of sparks and explosions in areas where there is a high concentration of flammable or explosive materials.
However, to make the most of their effectiveness and safety, it is crucial to understand how to properly store, use and maintain these tools. In this article, as subject matter experts, we will provide a comprehensive guide for those responsible for maintenance in mining environments.
Storage Recommendations
- Safe location: Non-sparking mallets should be stored in a dry, cool place to prevent corrosion or degradation of the material. Consider using brackets or hooks to keep them elevated and off the ground.
- Guard: To further protect them, keep non-sparking mallets separate from other tools to prevent damage to the head or handle.
- Avoid direct exposure: Continued exposure to sunlight or heat sources can compromise the effectiveness of the tool. Use opaque protective covers if you do not have adequate storage space.
Recommendations for Use
- Geometry: Before hitting, make sure the head of the mace is perfectly aligned with the point of impact. This ensures the effectiveness of the blow and reduces the risk of sparks.
- Surface: Inspect the surface before striking to ensure it is clean of flammable or corrosive materials that may increase the risk of sparks or damage the mallet.
- Angle: Maintain a 90° angle to the surface of the object to avoid uncontrolled bounces.
- Position of the person: It is essential that the operator maintains an upright and firm posture, with the feet apart to ensure proper balance.
- Hand position: Promote the use of heat and spark resistant gloves and ensure that the wearer's hands are at a safe distance from the head of the mace.
Maintenance and Inspection Recommendations
- Cleaning: Regularly wipe the mace with a dry cloth to remove debris. For persistent residues, consider using non-corrosive cleaning solutions.
- Inspection: Conduct regular inspections and keep records of inspection dates and any problems detected. If you find cracks, deformations or detachments in the head or handle, remove the mace immediately to avoid accidents.
- Do not machine: Emphasize that non-sparking mallets should not be machined or modified in any way, as any alteration may compromise their safety.
Recommendations for Tool Change/Discard
- Excessive wear: Set specific criteria for acceptable wear and replace the hub if it does not meet these standards.
- Compromised handle: If the handle shows cracks, detachments, or is loose, replace the entire tool. The safety of the tool depends on an intact handle.
- Ineffectiveness: If hitting produces sparks or does not achieve the desired impact, remove the mace immediately and replace it.
Other recommendations
- Training: Ensure that all users are properly trained in the safe use of non-sparking mallets, including identifying potential problems.
- Protective Equipment: Remind operators of the importance of always wearing safety glasses, gloves and proper footwear when using this tool.
- Exclusive Use: Do not use non-sparking mallets for purposes other than their intended purpose. Its design and material are specific to prevent sparks in hazardous environments.
In short, the safe use of non-sparking mallets is essential in mining environments where explosion risks are a constant concern. By following these storage, use, maintenance, and disposal recommendations, you can ensure these critical tools work effectively and help keep your equipment and workplace safe. Remember, safety should always be the number one priority in the mining industry.
Do you need to learn more about the safe use of industrial tools in mining environments? Consult our experts!