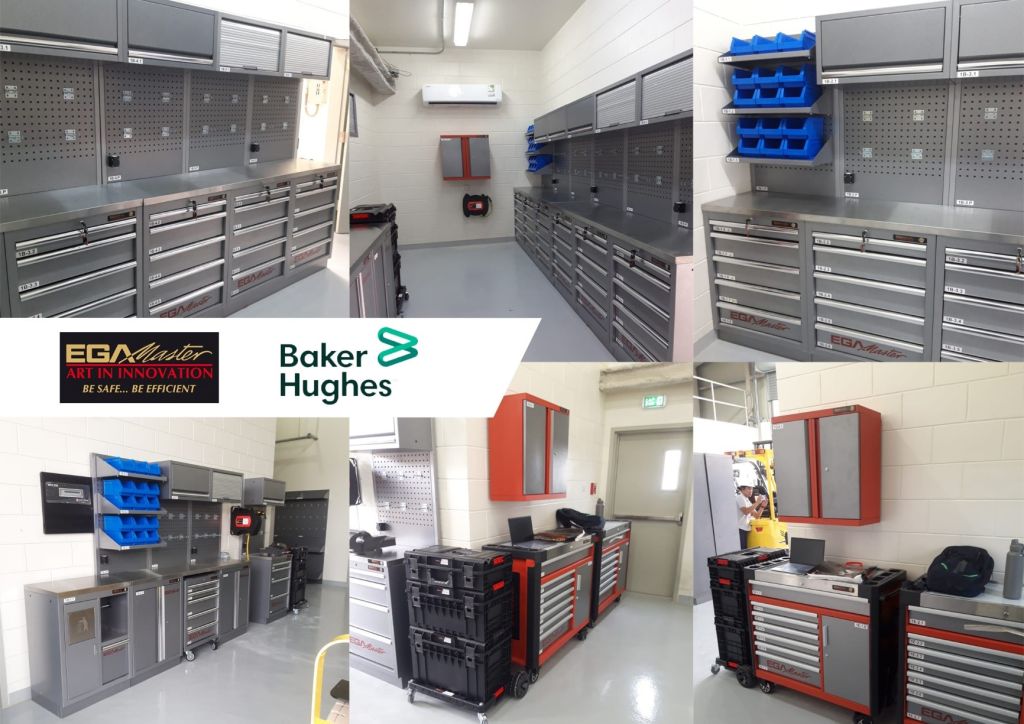
In the field of efficient management and industrial productivity, the 5S Method has established itself as a fundamental tool to improve the organization and the work environment. This system, originally from Japan and popularized for its effectiveness in various industries around the world, is based on five key principles.
In this article, we'll explore how to apply the 5S method specifically in tool organization, as well as the importance of having a single, nearby vendor to optimize the workspace according to the user's needs.
What is the 5S Method?
The 5S Method is an organizational philosophy that seeks to improve efficiency by creating an orderly, clean, and safe work environment. Each of the five steps plays a crucial role:
- Seiri (Classification): It consists of separating the necessary from the unnecessary. In the context of tools, it involves identifying and classifying the essential tools for each process.
- Seiton (Order): Once the tools have been classified, they must be organized in a systematic and accessible way. This facilitates quick location and efficient use during daily operations.
- Seiso (Cleaning): Maintaining a clean environment not only improves the image of the workshop, but also contributes to safety and accident prevention. In the case of tools, it involves cleaning and keeping them in good condition after each use.
- Seiketsu (Standardization): Establish standardized standards and procedures to maintain the first three steps (Classification, Order, and Cleanliness) in a consistent and sustained manner over time.
- Shitsuke (Discipline): Encourage personal and group discipline to follow established standards and maintain commitment to organization and cleanliness at all times.
Application of 5S in the Organization of Tools
When the 5S method is applied to tool organization, a significant improvement in operational efficiency and workplace safety is observed. Here are some key points:
- Classification: It is essential to identify which tools are essential for each process and which could be redundant or unnecessary. Not only does this reduce clutter, but it also makes it easier to quickly locate tools during operations.
- Order: Once the tools have been classified, they must be organized in a logical and systematic way. This can include the use of cabinets, shelving, and storage systems that facilitate quick and safe access.
- Cleanliness: Keeping tools clean and in good shape not only extends their life, but also improves efficiency by reducing time wasted searching for or repairing deteriorated tools.
- Standardization: Establish clear rules for how tools should be stored and how to keep the work area clean and tidy. This ensures that all employees follow the same procedures and contribute to a safer and more efficient work environment.
- Discipline: Foster a culture of responsibility and commitment to organization and cleanliness in the workshop. This is achieved through training, supervision, and recognition of employees who maintain high 5S standards.
Importance of Having a Single and Nearby Supplier
Having a single, nearby supplier that can design and install industrial tool furniture according to the user's specific needs is crucial to optimizing the workspace. Here are some key benefits:
- Customization: A specialist supplier in the user's sector can design tailor-made solutions that are perfectly suited to the space and the specific tools used in the workshop.
- Space Optimization: Well-designed industrial furniture maximizes the use of available space, facilitating the efficient organization of tools and equipment.
- Accessibility: Proper storage systems allow for quick and secure access to tools, reducing search time and improving productivity.
- Durability and Safety: Quality industrial furniture is designed to withstand heavy use and provide a safe working environment for employees.
The application of the 5S Method in tool organization not only improves efficiency and safety in the workplace, but also contributes to a more organized and pleasant work environment. Combining this approach with the right industrial furniture, designed by a specialist supplier, can significantly transform the working environment, making operations smoother and more efficient.
As an example, the cover image of this article (you can download it here) of the workshop we designed with the 5S approach, for the recently inaugurated Saudi Petrolite facility, a Joint Venture of the US energy company Baker Hughes.
Do you need to improve and optimize the organization and space of the maintenance areas?
Contact us for advice from our experts.