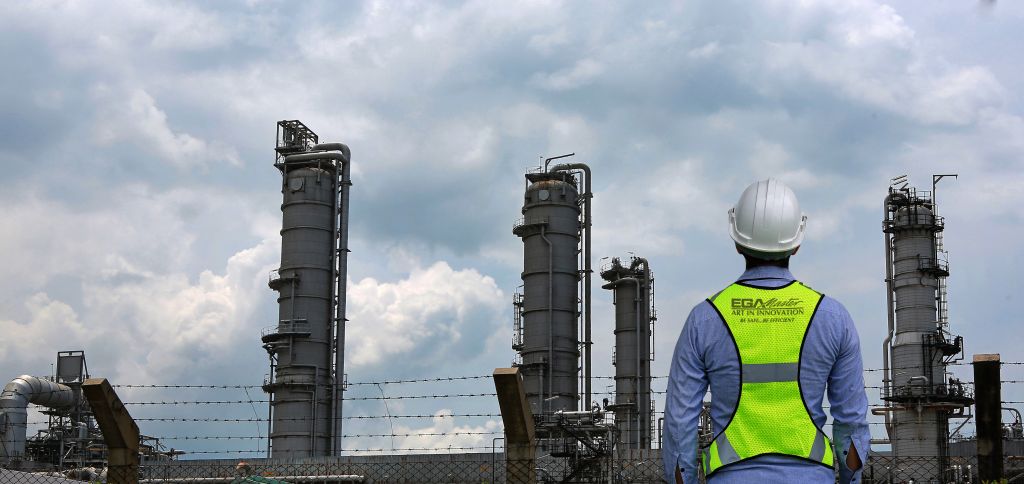
You can find the previous post here
Non-sparking tools
Life are problems ... But also solutions.
Non-sparking tools are those that generate low energy sparks, always below the ignition limit of those dangerous substances (gas or dust) present in the environment. The tools are called “non-sparking” if the temperature of the sparks emitted is below the lower limit of ignition, and they are therefore safe for use in explosive atmospheres.
The non-sparking tool offering is mainly divided into two categories:
- Copper-Beryllium (Cu-Be)
- Aluminum- Bronze (Al-Bron)
Of these two non-sparking alloys, the one with the most advantages is copper-beryllium.
Although it is worth 20-40 percent more than aluminum-bronze, it has superior mechanical and safety properties, making it the most profitable option in the long term. In addition, as it has a degree of hardness of 40HRC, it has a useful life of 40% higher than that of Al-Bron.
Consequently, the resistance of the non-sparking Cu-Be alloy is 50% greater than that of Al-Bron, therefore, it bears 50% more stress than the aluminum-bronze alloy. As the latter is a softer alloy, it needs to have 3% iron, making it a slightly magnetic non-sparking alloy and, consequently, the sparks they generate have more energy than the Cu-Be alloy, being the most recommended in explosive atmospheres type IIC.
Download our whitepaper to learn more about this topic
Which non-sparking alloy to choose? Cu-Be or Al-Bron?
Cu-Be non-sparking alloy is the best choice in 90% of the cases, as its better properties make it safer and more profitable.
Al-Bron is competitive if:
- The tool will be used infrequently, not periodically
- No great efforts will be made
- Total non-magnetism is not required
- It will not be used in explosive atmospheres of type IIC
If these four conditions are met, the best choice is Al-Bron non-sparking alloy. But if one of them is not fulfilled, better Cu-Be.
The explosive atmospheres generated by acetylene: the great exception
Acetylene is a group IIC gas, and therefore non-sparking alloys do not have the ability to cause it to deflagrate. However, this type of gas reacts with any alloy that is composed of more than 65% copper, where copper acetylide is generated.
As both Cu-Be and Al-Bron non-sparking alloys contain more than 80% copper, it makes the use of this type of alloys unfeasible in explosive atmospheres where acetylene is present.
ACETILEX: The EGA Master's solution
There are other non-sparking alloys other than Cu-Be and Al-Bron, such as brass. However, even though brass is made up of 60% copper, its mechanical resistance is very low compared to non-sparking copper-beryllium and aluminum-bronze alloys, specifically, between 4 and 6 times less mechanical resistance. This results in a shorter useful life, and in a very unprofitable option.
For this reason, at EGA Master we have developed ACETILEX non-sparking tools, which are non-sparking Cu-Be and Al-Bron alloys whose copper percentage is less than 65%,becoming the only safe and cost-effective non-sparking option in acetylene environments.
Take a look at our range of non-sparking tools and contact us