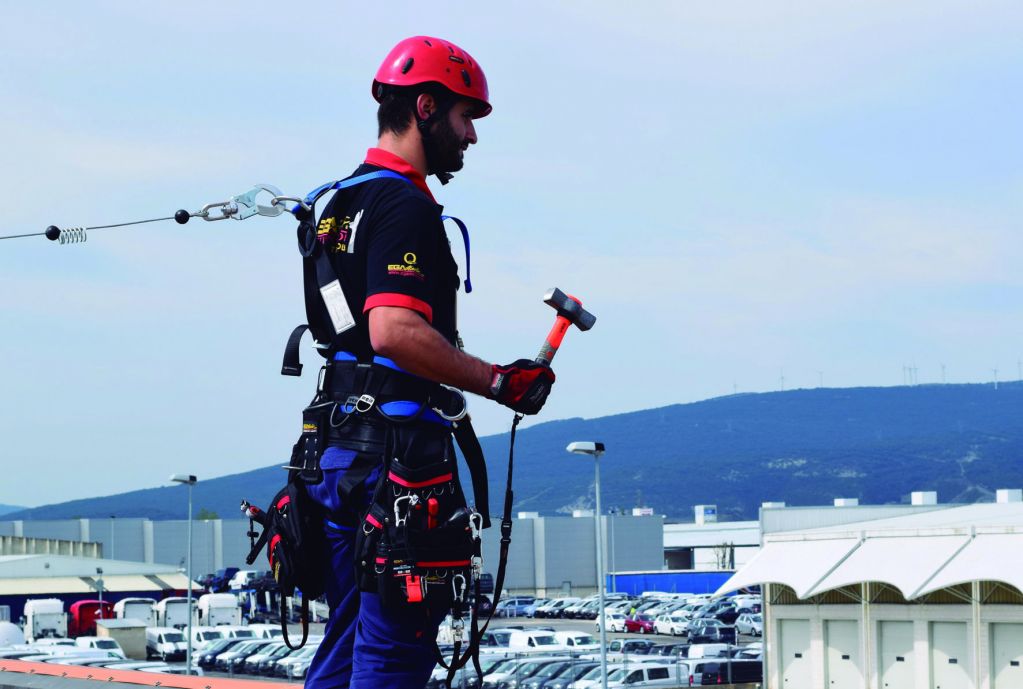
Previous Post: Accidents by Dropped Objects: More Common Than We Think
Common Causes of Incidents: Complacency, Incompetence, Lack of Supervision, uncertified or Damaged Fall Arrest Equipment, Operator Error, Poor Communication, Snagging and Collisions, Environmental Factors.
To avoid it, it is recommended the following:
The choice of equipment to be used should be made after evaluating the workplace environment.
Established control procedures should be followed before, during and after use.
Anyone using personal protective equipment against falls from height should have documented training (including rescue method training).
Nobody should work alone or unattended when using fall arrest equipment.
Everyone involved in the work scope should have enough training and awareness of the equipment and safety procedures A ‘Buddy’ check of all fall arrest, rigging and other equipment should be carried out. The necessary rescue equipment and trained personnel should always be available at the workplace.
Fall arrest equipment should comply with relevant national/ international standards, incorporate an anti-trauma safety device and comply with an accepted standard.
The equipment should be checked EVERY TIME before use and should be checked at least every 6 months by a competent person.
The date for next inspection should be clearly shown on the equipment.
The anchor point for suspension should be identified and rated to comply with relevant national /international standards, eg. OSHA.
Securing Tools <5kg / 11lbs
All use of tools at height should be risk assessed for suitability and for application (working environment, access, tool condition, competence of user, etc.)
All tools should be suitable for use at height and secured against being dropped whilst they are being carried to the worksite, used or stored at height (use tool bag with internal loops when several and / or heavy tools are required)
If an anchor point, other than the belt or bag is required, use an appropriate part of the surrounding structure, preferably above the work level. Tools heavier than 2kg / 4.5lbs should not be secured to the body, secure them to the adjacent worksite structure.
For work on or near rotating machines or travelling equipment, all tools should always be secured to the adjacent structure.
Attachment points / devices on tools and bags should be documentable (not all apertures on handles are actually rated tie-off points)
Lanyards on tools attached to the body should ideally be energy absorbing (fall damper)
The standard use of wrist lanyards is discouraged; however, it is recognized that they may be appropriate to specific tasks, eg within confined spaces.
Velcro wrist lanyards are discouraged where the integrity of the fastening may be affected by the work environment.
Tools used at height should be checked out / in in a register to ensure that nothing is left behind.
Proprietary tools for use at height and their retention components should not be modified. Using non-proprietary or modified tools, or alternative retention accessories may compromise integrity.
The use of socket wrenches is not recommended. The only advantage of them is to be able to exchange the sockets of different sizes; however, if they are used at heights, they must be fixed to the ratchet, so that they cannot be exchanged at heights. Thus, the socket wrenches lose their advantage of use over other wrenches, such as podging wrenches for structures, combination gear-wrenches, which in addition to be go-through, they are built in a single piece.
Next post: DROPS Recommendations:Securing Personnel (Part 2)