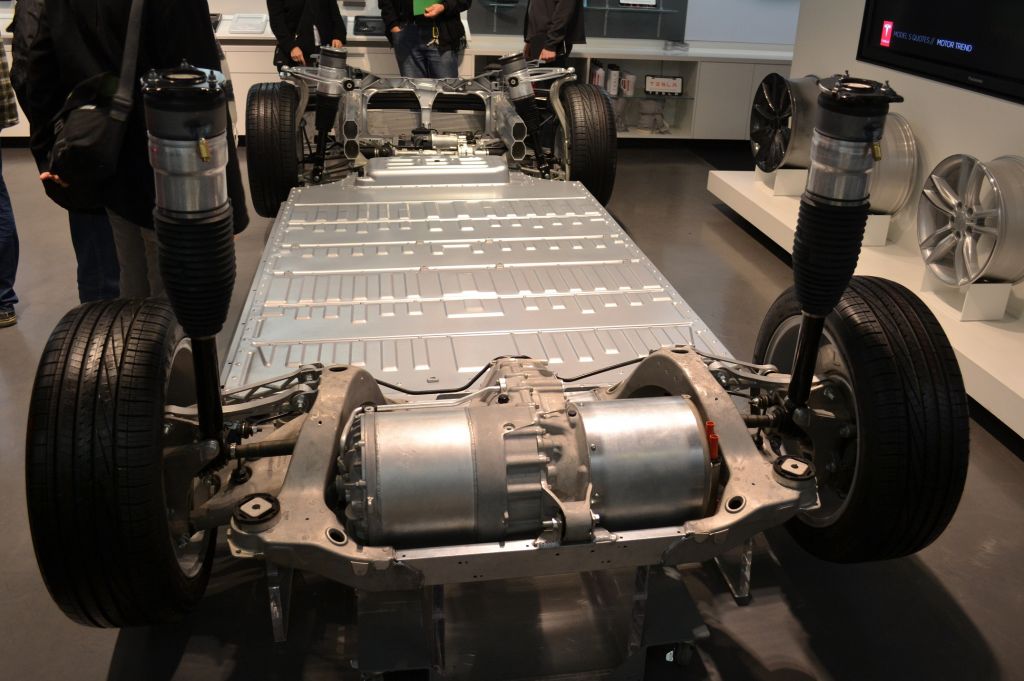
A couple of weeks ago, we were talking about titanium tools as a safe means of working safely in environments where high magnetic fields exist.
Among the places we mentioned in the previous post were the ones where synchronous engines are installed.
But what are synchronous engines? And how are they different from asynchronous?
Read on.
Synchronous and asynchronous engines, how are they different?
Synchronous engines have been around for decades, and so far, there has been no problem working in areas where they are installed, mainly because their dimensions have usually been reduced.
However, in sectors such as the naval, the electric vehicle, even the wind, involves the manufacture of this class of engines with a larger size.
Now, what risks are there when working on the assembly, maintenance and repair of synchronous engines? Do they also exist in asynchronous engines?
In both engines, the rotor rotates thanks to the electromagnetic fields that are generated around it. In the case of asynchronous ones, electromagnetic fields are generated in the stator area, which rotates at a slightly higher speed than the rotor (hence it is described as asynchronous).
Despite the existence of magnetism, this only occurs when the engine is running. So if there is a technical shutdown where maintenance and repair operations are required, normal steel tools could be used.
But this changes with synchronous motors, in which the electromagnetic field of the stator and the rotor go at the same speed (hence synchronous motor).
Although an electromagnetic field is also generated in the stator area, in the rotor there are permanent magnets, and therefore, even if the engine was in technical shutdown, that magnetic field would follow.
And here is the risk for the operator when working on it.
As we have said, synchronous engines have been manufactured for some time, but industries such as the naval demand engines of this class of enormous dimensions, where the rotor could even measure 2 meters in diameter.
And while the magnetic field of synchronous motors could be imperceptible 2 or 3 meters away, at a distance of less than one meter it is already beginning to be noticed.
We are talking about a force that any piece with a certain magnetism, for example, with a carbon steel tool, near this would attract it at a high speed, and would stick to parts of the engine, being almost impossible to remove it.
Now let's extrapolate this in case some operators are working on a synchronous engine.
Incorporating a carbon steel tool into that scenario would comprise a number of risks:
- That the tool flies out by the attraction of the magnets of the synchronous engine, being able to hit an operator that is around.
- That the operator who is working with this tool suffers serious injuries to the hand, because it has been trapped between the key and the magnet
Hence, for the naval industry, the manufacture of motors for electric vehicles, even for wind generators, we recommend the use of titanium tools.
However, it should not be believed that already by the fact of making an investment in these tools, all preventive measures have already been taken against working in environments with strong magnetic fields.
It is useless for me to go with magnetic titanium tools, if the car is magnetic
Find about our range of titanium tools and contact us.
If you need training, you can always for a seminar.
Picture Source: Creative Commons. Tesla Motors Model S