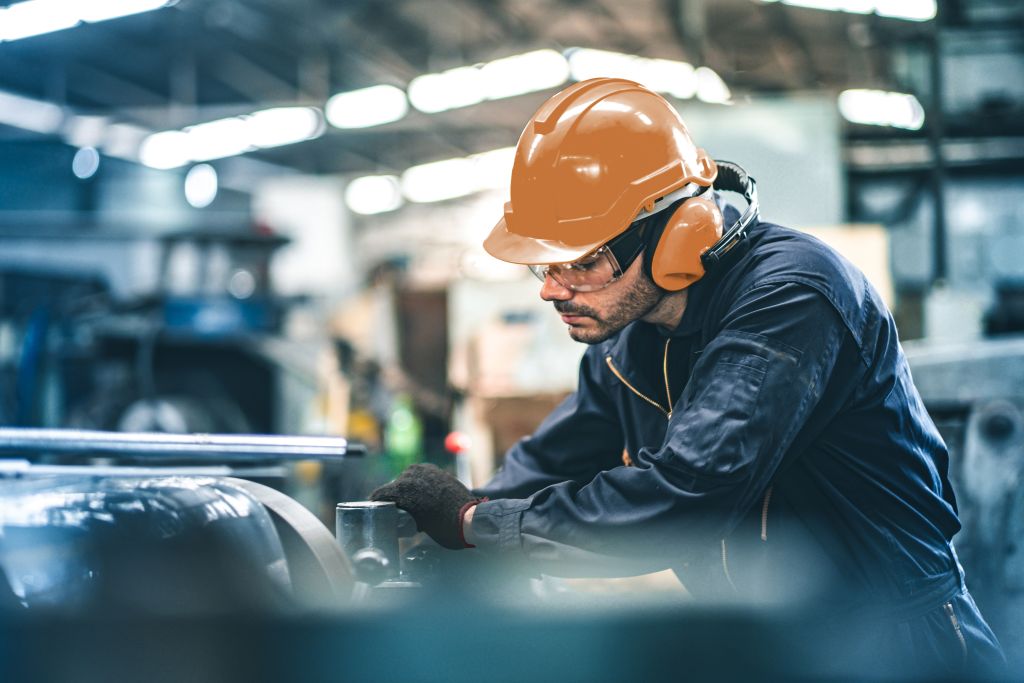
The hand tool is a means that is used in all sectors of all industrial activities, so the number of workers exposed to them is very high.
Injuries with tools, in general, are usually, or can become, mild.
However, there are serious accidents that cause permanent disabilities.
That is why the principles of safety are important, not only for the tool, but for the user itself as well.
To begin with, it is essential, before carrying out the work, to recognize the environment, to know where there may be risks of:
- Falls
- Stumbling
- Not reaching well the position that can make us lose our balance
- The operator dropping something
This must be analyzed, depending on the time we spend in that area. Therefore, depending on the latter, a more or less exhaustive analysis must be made.
Obviously, there are more variables to analyze as we have explained above, for example, if there is a railing where the operator is going to lean, is that structure really in conditions to hold its weight?
What are the basic safety rules in tool use?
We will give 4 rules that have to be applied on a daily basis. We seethe:
- Use approved PPE , for example:
- Wearing glasses in case something might jump into the eyes
- Wear a helmet if there is a risk of an object falling on the operator
- Use masks if there are harmful environments
- Use the right tool, and use it correctly:
- For example, using a hammer and not the head of a screwdriver to perform striking operations
- Use a 1000V insulated tool in high voltage environments, and not an uninsulated tool.
- Maintain the tool on a regular basis
- Certainly, there is little maintenance to perform on a tool, but it is important to keep it well, try not to rust. And in case of rust, take it into account, because if the degree of rust is already advanced, it is at risk of breaking when used for a job.
- Have a tool control system
It is important to have adequate tool control systems, which will depend on:
- The type of operation to be performed
- The level of risk or severity that exists
For example, if the maintenance is always done by the same operator, probably the best tool control system is a set of foam trays, with the silhouettes of these tools marked on them.
Why? Because being the same operator, you can easily identify which tools are missing and never forget.
And in an assembly line where there are several operators involved distributed by work shifts? A tool control system with software is likely to be required, which identifies:
- What tools should be used for that operation
- What tools are missing if that situation occurs
- Who has used these tools
In the next post we will talk about what are the most common risks and accidents, when using an industrial tool.