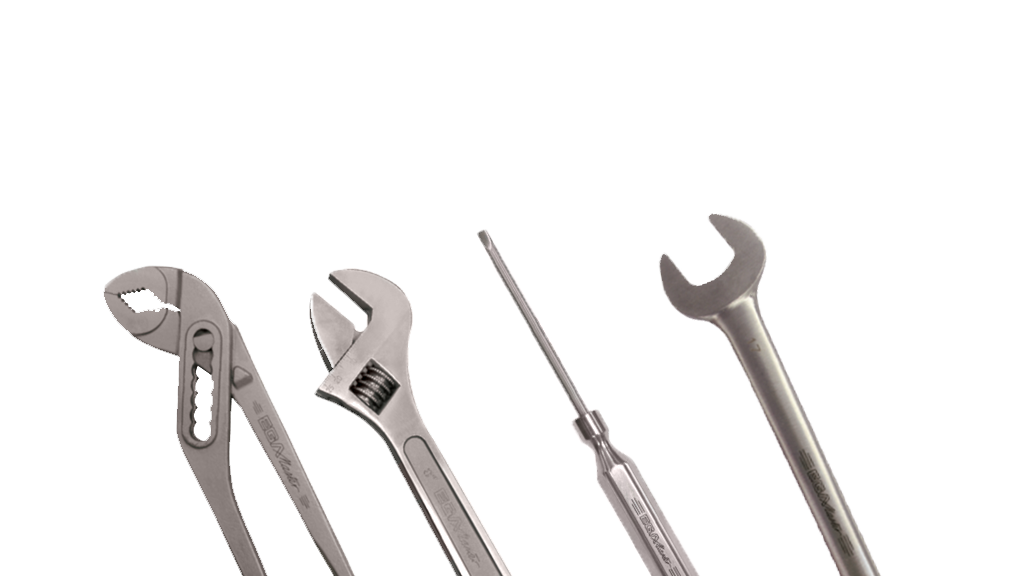
We come to the final chapter of our stainless steel saga. We have already talked about the properties of this material, how to use industrial tools made with it, and what selection criteria should be followed.
Today we talk about why we have selected 420 stainless steel for the manufacture of our tools.
You want to know why? Keep reading!
There is a variety of stainless steel alloys in the world: 201, 204, 304, 316, 409, 439…
Why choose one?
Properties of 420 stainless steel compared to other alloys
Grade 420 Stainless Steel has mechanical features very similar to those of carbon steel, which makes it possible to manufacture tools whose mechanical characteristics are close to those of industrial use tools.
It has a reasonable oxidation resistance.
There are other alloys that have better resistance to oxidation, which are grades 304 and 316 stainless steels.
The question now is: If they are better stainless steels, then why do we prefer to manufacture with grade 420 stainless steel?
Because the tensile strength and hardness of grades 304 and 316 stainless steels are worse than 420.
In other words: they do not have a valid hardness for an industrial tool, nor for a manual tool.
In fact, it rarely makes sense to make tools with 304 and 316 steels, because with intensive use of these, it will cause rapid wear, or even breakage.
Regarding non-magnetism, grade 420 stainless steel is not, since it is a martensitic-ferromagnetic alloy, so industral tools made of said alloy cannot be used in environments where there are strong magnetic fields.
It is a disadvantage from that point of view.
And it also turns out that austenitic stainless steels (grades 304 and 316) are non-magnetic since they have another internal crystallography.
It seems that the austenitics are full of virtues: better resistance to oxidation, and above all, non-magnetic.
Shall we say goodbye to the more expensive titanium tools?
No. Let's remember: austenitic stainless steels have the great disadvantage that, from the point of view of the industral tool, their hardness is very low (15 HRC compared to 33-43HRC that titanium has).
So, there is no comparison.
And if titanium has 900 Nm2, stainless steels grades 304 and 316 can be around 300 Nm2.
In summary, if we allow ourselves to be convinced by the apparent advantages of non-rusting and magnetism of these alloys, when using a tool made with them, it will happen that:
- They will wear out very quickly and will have to be replaced frequently
- If they are used in jobs where a high torque force must be applied, they will end up breaking because they have less resistance.
It is true that, from the point of view of the stainless aspect, grades 304 and 316 stainless steels are a better option in some specific processes, especially sterilization.
But in general, from the industrial tool point of view, we have to be pragmatic and select the correct stainless-steel alloy.
We have to be aware that these tools are going to be exposed to frequent use, carrying out tightening at high torques, etc.
That requires adequate hardness and tensile strength.
And that's what makes us select grade 420 stainless steel.
It is not the best, but as we have already said, it has reasonable stainless properties that for most applications is sufficient. And, in addition, it provides the best mechanical properties of all stainless steels.
Having said all of the above, we can now clarify two confusions that they usually have regarding stainless steels:
- That all the stainless steel tools are non-magnetic. No, it is not. Our grade 420 stainless steel is not because it is martensitic.
- Compared to titanium, obviously austenitic stainless steels, which are grades 304 and 316, which can have important non-magnetic properties, are not as good as titanium, but for many applications they can be valid. But it is not equivalent to titanium.