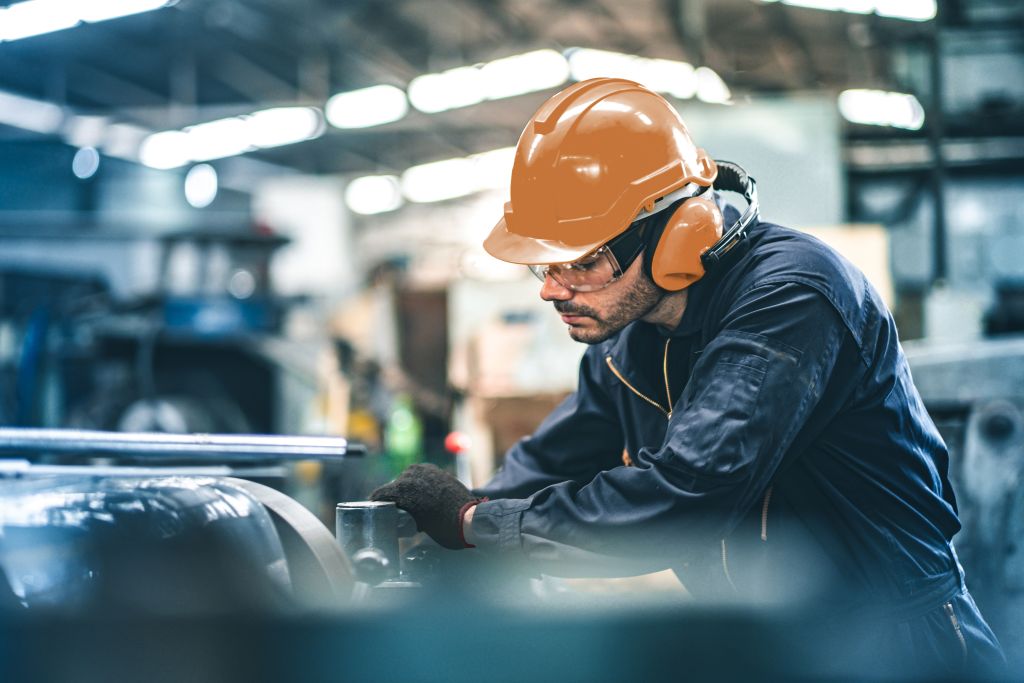
In the previous posts, we were analyzing the basic safety rules that must be taken when using industrial tools.
We also saw what are usually the most common accidents and their causes.
Today, we're going to take a look at some steps that can be taken to prevent, or reduce, these risks.
On the one hand, we will expose the preventive measures to follow in the use of tools and, on the other, those that can be taken to avoid accidents caused by the misuse, or abuse, of industrial tools.
What are the preventive measures to follow in the use of the tool?
Among them are:
- Make a suitable selection in the acquisition of industrial tools
- Do not use extensions on fixed or combined wrenches
- Respect for the safety practices associated with its use such as:
- Do not put your hand near the tip of the screwdriver while the tightening operation is being performed, as the screwdriver may slip and cause serious hand injuries
- Do not place your hand on a slogging wrench
- Turn off the electrical voltage before working on a circuit or electrical network, even having 1000 volt insulated tools
Plus, it should:
- Implement a tool acquisition management program
- Training in control and storage of industrial tools, both for safety and economic efficiency.
- Introduce a plan for the disposal of tools: very important, since, normally, what is done is to save them, creating the possibility that an operator will use it in the future, with the risks that this entails.
What are the preventive measures to avoid accidents in the use of industrial tools?
First, have ergonomic and quality tools that are proportional to the dimensions of the user.
They also must be appropriate to the strength and resistance of it, because if the user does not have enough strength, to get a nut released with a normal combined wrench, it will surely have to use an extension wrench, and thus apply greater lever.
Have tools that reduce user fatigue: important to avoid not only fatigue, but also joint and muscle injuries.
The importance of tool design criteria
As an extra to the recommendations, we have given above, we also want to emphasize the importance of the tool design.
This must be adapted to most of the population.
The design of the tool should allow the wrist to remain straight during the performance of the work.
If the wrist is not in a correct position, the operator may develop injuries in areas such as the carpal tunnel.
Special emphasis must be placed on the design of the handle of the tool, since, probably, it is the most significant part, because it is the one that interacts with the operator.
This raises the importance of the handle being well attached to the hand, avoiding generating pressure in it, and allowing correct positions when working.
In the next posts we will show the solutions we offer from the EGA Group, as support for preventive measures to help the safety and efficiency of operators, in the performance of their work.
And if you can't wait, write to us, and we will give you advice on the safe use of the tool.