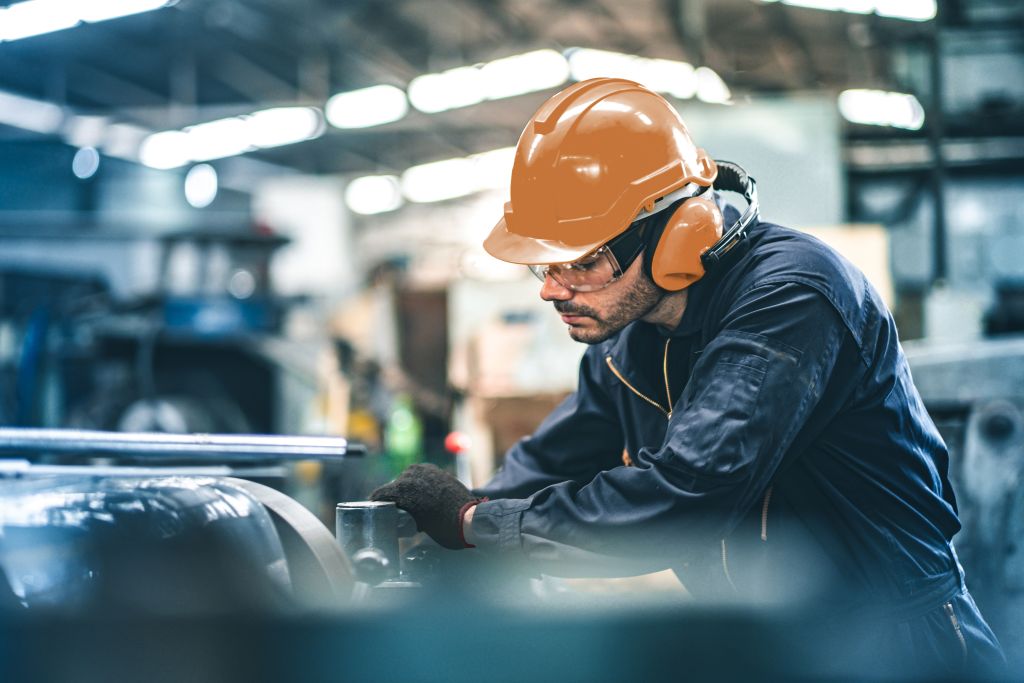
As we promised in the previous post, we finished this saga on the "Safe use of tools", with the solutions we have developed in the EGA Group for some of the aforementioned cases.
Solutions for explosive atmospheres
We will not go into detail in this section, since at the time we already announced the solutions we manufacture for explosive environments, even so, we invite you to take a look at the section we have of Safety in Explosive Atmospheres
Solutions for working in environments with magnetic fields
As in the case of explosive atmospheres, we made a post where we talked about the alloy we use to make our amagnetic tools.
Solutions for Striking Hazards
These risks occur mainly with slogging wrenches.
When the operator needs to tighten by means of a slogging wrench, the turn is done by hitting said wrench.
The problem is that, for the operator to perform the tightening correctly, he needs to hold the wrench while hitting, to prevent it from falling, since there is clearance between the wrench and the nut. This increases the chances of hitting his hand while doing the job.
What we did in the EGA Group, was to take a slogging wrench, we made a groove where we introduced an O-ring, reducing the degree of slack, and that added to the degree of friction it has, preventing the wrench from jumping when hit.
In addition, we put a removable shackle on the handle, making it antidrop®.
This is how the total safety slogging wrench was born, which was awarded in 2019 as the most innovative product at the NSC Safety Congress in San Diego (USA).
Solutions in case of falls and losses of balance
There are situations, for example, when working with pipe wrenches where the operator usually needs to use both hands.
Why? Because with one he must hold the wrench, and with the other the nut.
As the nut is adjusted, the operator approaches the tube, and this inclination of the operator may cause him to lose his balance.
That's why we developed the MASTERGRIP.
Among its many other advantages, from the point of view we address here, is that it can be always used with one hand. Why does safety increase? Because with the other hand, if the operator is working on a ladder, it allows him to be supported or holding on to some fixed element, so that it makes it more difficult for him to lose his balance.
Of course, it is not the only solution we offer, we already talked about our developments for work at height.
Solutions for part detachment
A case that we have seen on a regular basis is the detachment of hammer heads.
The heads of the hammers are attached to the handles in different ways.
For example, in wooden handles wedges are used, resins are used, so that the fastening between the handle and the head is strong and durable.
However, being a union, it has a shelf life, which will depend on how it is preserved and how it is used, as well as the frequency of use.
That is why we recommend that, before using them, users perform a pre-check work, to ensure that there is no clearance between the head and the handle, because if there is, the inertia in the action of the blow can cause the head to be fired at a considerable speed, hitting people or critical elements (gas pipes, compressors...)
Since virtually no one does this pre-use check, we have increased the safety of using hammers and mallets through simple solutions, including:
These are used in some fiberglass mallets, so that it is impossible for the head to be dismissed, since the upper part of the handle that protrudes from the head is wider than the hole where it is embedded.
In addition, the more it is used, the more the head will remain embedded in the handle, thus increasing the degree of support.
It is not convenient that all hammers are made with a handle that protrudes from the head.
This is so, because there may be cases where there are surfaces close to the hitting zone, thus reducing the margin of maneuver.
What solution have we developed for these cases?
A through hole is made to both the head and handle, where a safety pin is placed.
The objective is not to continue using the hammer once the head has slack, but once it has it and it has not been detected, the pin prevents the head from being thrown off in the middle of the work that the operator is doing.
So far this saga about the safe use of industrial tools.
If you want to delve deeper into this topic, we invite you to write to us to contact our experts. We will be happy to support you.